Every industry faces this same question, and several aspects come into play to determine what the best approach is. When you boil it all down, the most likely decision maker will be Cost.
However, cost is not as straight forward as you might think. There are several aspects to this such as loss of production, human Cost (OH&S), risk to others, and materials cost and time. Each of these has a different cost that has to me measured in a different way.
Table 1 outlines the different approaches and the different outcomes.
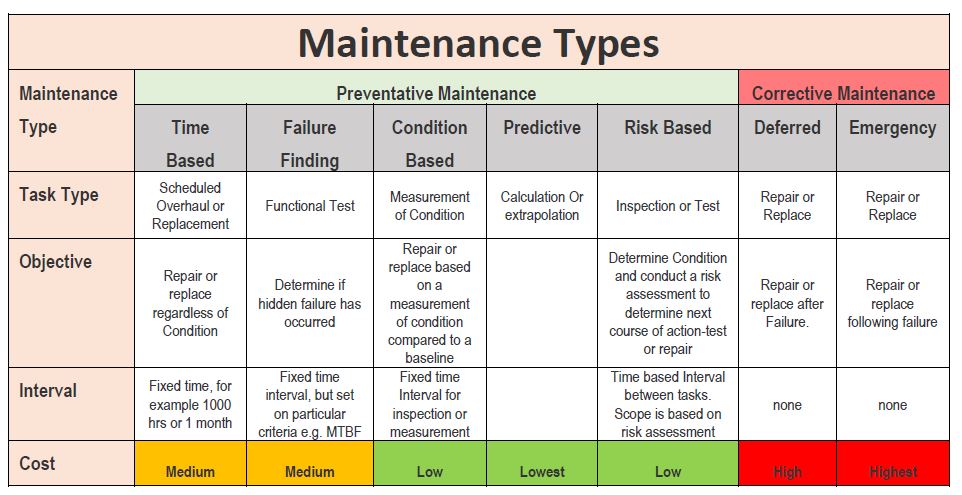
Time-Based Maintenance
Time-Based Maintenance refers to repairing or replacing an item to restore its reliability at a fixed time, interval or usage regardless of its condition, this is also known as scheduled maintenance. The purpose of Time Based Maintenance is to protect yourself against the failure of wearing parts which have predictable Mean Time Between Failure (MTBF). Time Based Maintenance assumes that the failure is age related and a clear service life can be determined.
Failure Finding Maintenance
Failure Finding Maintenance tasks are aimed at detecting hidden failures typically associated with protective functions. Items like safety valves, secondary systems, and emergency functions.
This type of equipment won’t be required to function until something else has failed. That means that under normal operating conditions you will not know whether this equipment is still functional as the failure modes are hidden. Because these failures are hidden, you’ll need to repair the failure before you are relying on that equipment to protect you.
It’s important to realise that failure finding maintenance tasks do not prevent failure but simply detect it. And once detected you’ll have to repair the failure you found. Failure Finding Maintenance is conducted at fixed time intervals typically derived from legislation or risk based approaches.
Condition Based Maintenance
Condition Based Maintenance relies on the principle that most failure modes are not age related. However, most failure modes do give some sort of warning that they are in the process of occurring or are about to occur.
If evidence can be found that something is in the early stages of failure, it may be possible to take action to prevent it from failing completely and/or to avoid the consequences of failure. Condition Based Maintenance as a strategy therefore looks for physical evidence that a failure is occurring or is about to occur. Thinking of Condition Based Maintenance in this way shows its broader applications outside condition monitoring techniques often only associated with rotating equipment. This methodology can be applied to many areas for example brakes, suspension and emissions.
It is important to realise that Condition Based Maintenance as a maintenance strategy does not reduce the likelihood of a failure occurring through life-renewal, but is aimed at intervening before the failure occurs, on the premise that this is more economical and should have less of an impact on availability.
Predictive Maintenance
Predictive Maintenance up until recently was essentially another name for Condition Based Maintenance. But with the advent of Artificial Intelligence, much lower costs of equipment sensors and machine learning there is clearly a difference appearing between Predictive Maintenance and Condition Based Maintenance.
Predictive Maintenance is a good extension, and a more advanced approach to Condition Based Maintenance where we use potentially many process parameters gained from online sensors to determine if the vehicle is moving away from stable operating conditions and is heading towards failure. The central idea here is to predict when the failure is going to occur and then determine the appropriate time for maintenance intervention.
Corrective Maintenance
Corrective Maintenance strategy only restores the function of an item after it has been allowed to fail. It is based on the assumption that the failure is acceptable (i.e. no significant impact on safety or the environment) and preventing failure is either not economical or not possible.
Apart from being the outcome of a deliberate Run to Failure strategy Corrective Maintenance is also the result of unplanned failures which were not avoided through preventive maintenance. A run to failure strategy can effectively be used where the consequence of failure is limited and would not necessitate a need for an urgent repair.
Emergency Maintenance
Emergency Maintenance is corrective maintenance that is so urgent that it breaks into your Schedule. It upsets your plans and schedules and typically throws everything into disarray. Some people thrive in this type of environment and often get heralded as heroes when they have worked 16hrs non-stop to get the vehicle back in service. But when it comes to Reliability it is a dead end.
So Emergency Maintenance is the one and only maintenance type that we really want to avoid as much as possible. In fact, World Class organisations ensure that less than 2% of their total maintenance is Emergency Maintenance.
Generally speaking, unplanned corrective maintenance i.e. Emergency Maintenance is the most expensive to conduct. This is because this type of maintenance does not go through the full maintenance planning & scheduling process because it’s so urgent and it’s simply planned on the fly. That means when you execute Emergency Maintenance you typically have very low efficiency with additional time wasted looking for materials, organising access to the equipment, waiting on other trades etc. Another common issue with Emergency Maintenance is that often parts and services are expedited to arrive faster and increased costs are incurred to make that happen.
Prevention of a failure is simply a lot cheaper and safer than letting equipment fail. Plus, preventive maintenance would have much less impact on serviceability than breakdown maintenance (i.e. running to failure).
Which Is Better: Preventive Maintenance Or Predictive Maintenance?
Predictive Maintenance really is a type of Preventive Maintenance as they both see you conducting maintenance before the failure has occurred. The issue is though that most people think of the traditional Time-Based Maintenance when they talk about Preventive Maintenance.
So from that perspective which is better? You need to select the right maintenance type based on the failure mode you’re trying to manage and its characteristics. If you have a failure mode that is random in nature you would want to opt for a condition-based or predictive maintenance task so that you can see the potential failure coming closer and take action before the failure occurs. Brakes, suspension and oil easily fit into this category.
However, if you have a failure mode that is very clearly age-related or where a condition based task is simply not economical then you would use a time-based maintenance task. Examples in this category would be consumables such as filters and lighting.
AutoTest Testing Equipment
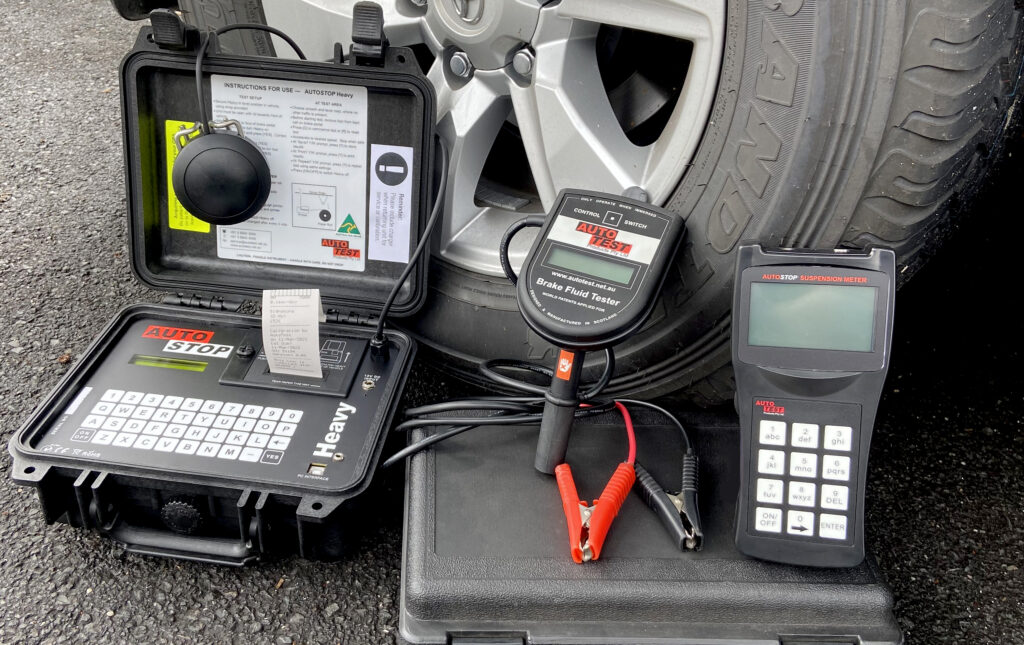
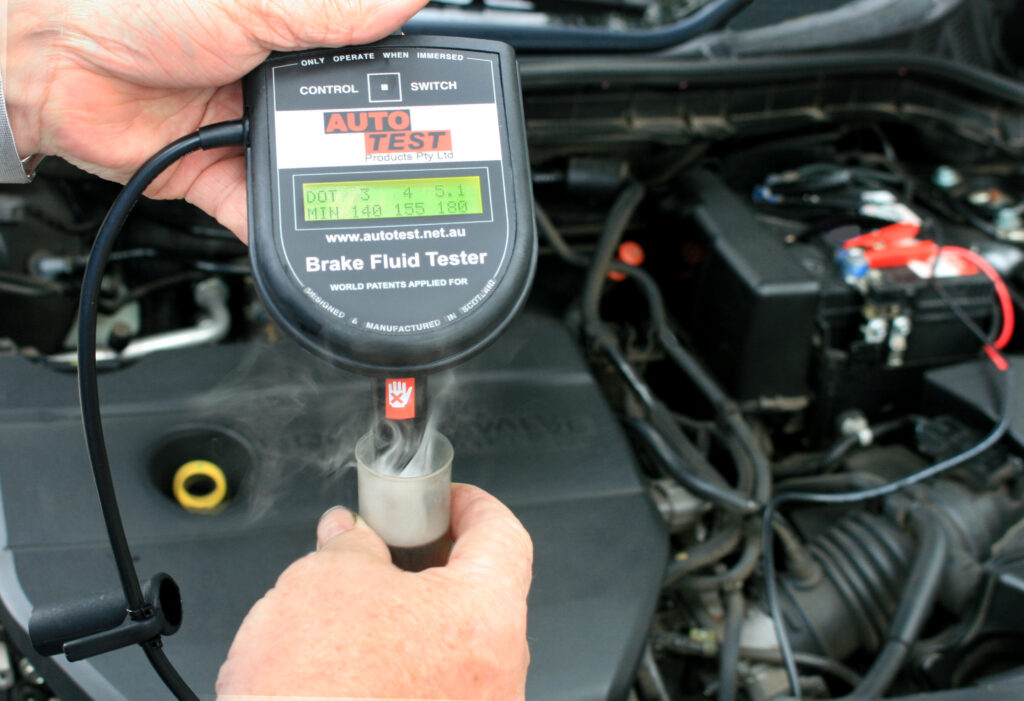
AutoTest provides equipment to reliably test all aspects of a vehicle. Selling a range of Decelerometers for testing the whole brake system, a Brake fluid tester for testing the brake fluid and a Suspension meter for testing the shock absorbers, Emission analysers for fuel tuning and gaseous emissions, headlight, battery noise and windscreen equipment.
AutoTest Products Pty Ltd is an Australian Made and Owned, award-winning manufacturer and distributor of state-of-the-art automotive testing and diagnostic products located in the Kensington, Victoria. Our products are designed to provide you with many years of reliable testing and are built from durable quality components. AutoTest’s product range includes a combined Gas and Opacity analyser, a range of AutoStop brake performance meters and calibrator, the AutoStop suspension meter, the AutoTest eNoise sound level meter, the AutoTest acoustic calibrator, the AutoLight light transmission meter, a brake fluid tester, and battery analyser.
AutoTest products are used by garages, workshops, regulatory authorities and service testing stations. AutoTest supply directly and through a network of international distributors located in Australia, Asia the Pacific Islands, Europe, Africa and the US.
AutoTest’s new product development program ensures the consistent launch of innovative, new products designed to meet the needs of the automotive industry and changing vehicle safety regulatory requirements.